It is one of the most commonly employed calibration instruments in the process industry. Regular calibration is a crucial process because these are mechanical instruments. Therefore, they are liable to drift off due to mechanical stress.
Calibration of such instruments is a significant process. Hence, it has to be done with extreme care rather than by calibration professionals. Therefore, below are the 5 most important aspects to keep in mind for the calibration process:
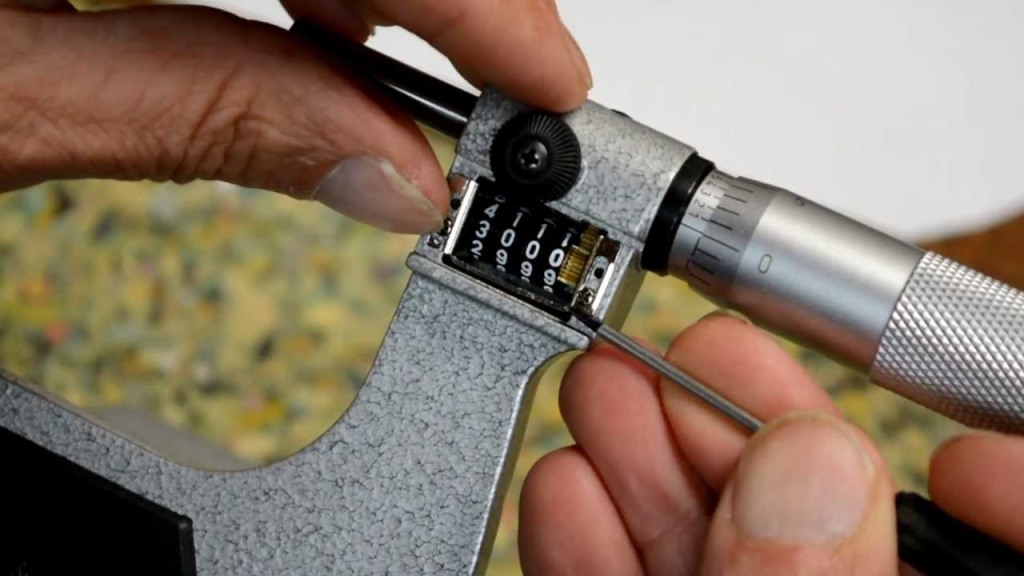
- Classes of Accuracy— It is important to understand the visible accuracy class of the instrument during the process. In most trials, the accuracy class indication is the ‘% of latitude.’ This implies that if the accuracy class is One Percent & the scale range is maybe zero to 100 psi, the accuracy is +-1 psi. Therefore, it is essential to know the accuracy class of Od Micrometers. It is because it will help specify the acceptable accuracy level and effect of other calibration methods.
- Pressure Medium Used— A gas or a liquid is one of the most typically used pressure tools for calibrating. Gas is ordinary air, and the selected liquid is either oil or water. The selection of pressure media relies on the tools that are being used in the procedure. Thus, they pertain to the instrument being calibrated. The choice also relies heavily on the pressure range.
- Contamination— Pressure tools used for calibration should not incline to contamination. Dirt is a familiar contaminant in such cases, and it could be existing inside the gauge, which could disrupt the procedure and distress the calibration equipment.
- Height Difference— The height of the meter that is being calibrated and the height of the calibration tool should be assessed before beginning the Pressure Gauge Calibration process. This is vital because the elevation difference can inflict an error due to the hydrostatic pressure of the pressure instrument. In such cases, it’s impossible to fix the equipment and the gauge at the Semantic height. Thus, the outcome of the height discrepancy should be subtracted and noted during calibration.
- Leak Testing— Before inaugurating the calibration, it is crucial to perform a leak test of the piping. If any leaks are existing, they may offer a way to errors. An easy leak test is to pressurize the system, then let the pressure settle. The pressure should be controlled during this test to confirm that it doesn’t drop too much.
EndNote
Besides these five steps, other factors and steps should be considered while placing pressure instruments for calibration. However, for primary testing, these five will do a sufficient job. Thus, follow carefully.